Automated Systems in Manufacturing
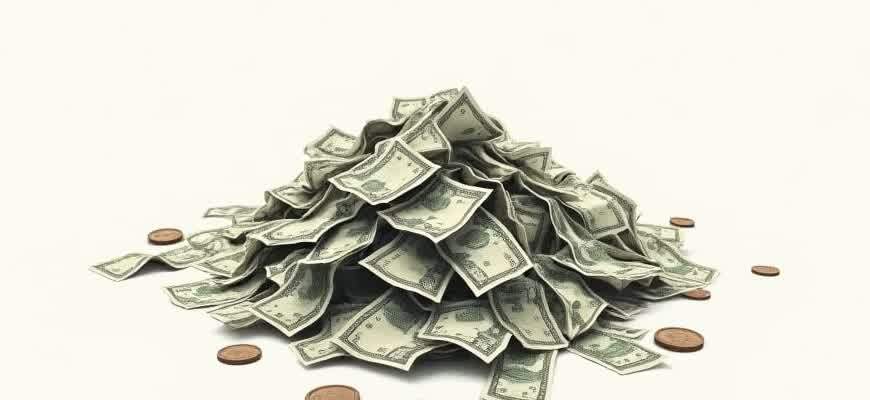
The growing demand for automation in manufacturing industries has led to the integration of various advanced technologies, including blockchain, to improve production processes, enhance efficiency, and secure data. These automated systems, powered by artificial intelligence (AI) and machine learning, enable real-time decision-making, predictive maintenance, and streamlined operations. When combined with blockchain, these systems can create decentralized, tamper-proof records, offering transparency and security throughout the manufacturing lifecycle.
Key benefits of automated manufacturing systems integrated with blockchain include:
- Improved data integrity: Blockchain ensures that all production data is recorded in a secure and immutable ledger, preventing tampering and unauthorized access.
- Enhanced supply chain visibility: Real-time tracking of goods and components is made possible, reducing errors and ensuring the authenticity of products.
- Cost reduction: Automation reduces human intervention, leading to lower operational costs, while blockchain minimizes the need for intermediaries and paperwork.
Blockchain technology in manufacturing ensures that all transactions are transparent and traceable, which is critical for industries dealing with high-value goods or sensitive materials.
Some of the notable applications include:
- Smart Contracts: Automatically executed agreements between manufacturers and suppliers, reducing administrative overhead and ensuring compliance.
- Product Lifecycle Tracking: Continuous monitoring and recording of a product's journey from raw material to finished good.
Feature | Impact on Manufacturing |
---|---|
Automation | Reduces human error and increases production speed |
Blockchain | Ensures transparency and traceability of manufacturing processes |
How Automation Enhances Efficiency and Quality in Manufacturing
Automated systems in manufacturing not only streamline production processes but also significantly improve speed and the overall quality of output. By implementing robotic arms, AI-driven quality checks, and real-time data analytics, factories can operate at an optimized pace. This helps manufacturers meet market demands faster while maintaining a consistent product standard. The introduction of automation into key stages of production enables continuous, uninterrupted operations, reducing human error and variability, which directly contributes to superior end products.
Automation’s impact is particularly evident in industries that require precision and high throughput, such as electronics and automotive manufacturing. By integrating advanced technologies, the production speed can increase significantly, while at the same time, the quality assurance process becomes more rigorous. With minimal manual intervention, automated systems can continuously monitor performance, identify deviations, and make necessary adjustments without slowing down production lines.
Key Advantages of Automation in Production
- Increased Production Speed: Automated machines can work at a faster pace compared to human workers, leading to higher output volumes within shorter timeframes.
- Enhanced Quality Control: Automated systems equipped with sensors and AI can detect flaws and inconsistencies more accurately than manual inspections, ensuring high-quality products.
- Reduced Downtime: Robots and automated tools can perform maintenance tasks or switch between production stages seamlessly, minimizing downtime and keeping the system running continuously.
Impact on Product Consistency
In a highly competitive manufacturing environment, consistency is key to maintaining a strong market presence. Automated systems excel in ensuring that every unit produced meets the exact specifications, reducing variations in the final output.
"Automated quality control systems allow for the continuous monitoring of every unit, ensuring that production standards are adhered to with minimal fluctuations."
This consistency not only boosts consumer trust but also improves overall efficiency by eliminating the need for rework or waste, which can be costly both in terms of time and materials.
Production Performance Comparison
Metric | Manual Process | Automated Process |
---|---|---|
Production Speed | Moderate | High |
Quality Control | Inconsistent | Precise |
Downtime | High | Low |
Operational Costs | Variable | Stable |
Key Technologies Behind Manufacturing Automation: Robotics, AI, and IoT
In recent years, the manufacturing industry has undergone a transformation driven by the integration of cutting-edge technologies. The shift towards automation is primarily facilitated by three key innovations: robotics, artificial intelligence (AI), and the Internet of Things (IoT). These technologies work in tandem to improve efficiency, enhance precision, and reduce human error, thus pushing the boundaries of what is possible in modern production systems. The emergence of these advanced tools has reshaped traditional manufacturing processes, enabling smart factories and interconnected systems to optimize production workflows.
Robotic systems are at the forefront of this automation revolution, taking over repetitive and labor-intensive tasks. AI algorithms power the decision-making capabilities of machines, allowing them to perform complex tasks autonomously. Meanwhile, IoT facilitates real-time data exchange between devices and systems, enabling predictive maintenance and process optimization. Together, these technologies form the backbone of Industry 4.0, which focuses on interconnected, intelligent, and self-optimizing manufacturing environments.
Robotics
Industrial robots have become integral components in manufacturing, enabling high-speed, high-precision assembly, welding, and material handling. Their ability to perform repetitive tasks with minimal human intervention has revolutionized production lines. These machines are capable of working in hazardous environments, improving safety, and reducing costs.
- Precision and Speed: Robots operate with high precision, ensuring products meet stringent quality standards while maintaining high throughput.
- Flexibility: Modern robots can be easily reprogrammed to perform different tasks, offering adaptability in dynamic production settings.
- Safety: Robots can work in hazardous conditions, preventing injury to workers and minimizing human exposure to dangerous environments.
Artificial Intelligence (AI)
AI technologies allow machines to learn from data, make decisions, and adapt to changes in real-time. In manufacturing, AI is used to improve operational efficiency through predictive analytics, quality control, and process optimization. By utilizing deep learning, AI can enhance the capabilities of robots and autonomous systems.
- Predictive Maintenance: AI predicts equipment failures by analyzing historical data, reducing downtime and repair costs.
- Quality Control: Machine learning models can detect defects in products during production, ensuring that only high-quality items are shipped to customers.
- Optimized Scheduling: AI-driven systems optimize production schedules by dynamically adjusting to shifts in demand and supply chain conditions.
Internet of Things (IoT)
The IoT allows manufacturing systems to connect and communicate with one another in real time. Devices embedded with sensors collect vast amounts of data, providing insights into the health of machines, inventory levels, and production performance. This constant data flow enables manufacturers to make informed decisions and improve overall efficiency.
"IoT-based systems can reduce operational costs by enabling real-time monitoring, improving asset utilization, and facilitating predictive maintenance."
IoT Benefits | Manufacturing Impact |
---|---|
Real-time data collection | Improved decision-making and faster response times to operational issues. |
Predictive Analytics | Minimized downtime and optimized machine performance through early fault detection. |
Remote Monitoring | Ability to oversee and manage production processes from any location, reducing the need for on-site personnel. |
Integrating Cryptocurrency Solutions with Automated Systems in Manufacturing
Manufacturing processes, traditionally dominated by manual labor and simple machinery, are increasingly evolving with the introduction of automation. However, integrating advanced systems, particularly those leveraging cryptocurrency technology, presents unique challenges and opportunities. A key consideration is ensuring seamless communication between existing infrastructure and newly implemented automated solutions, which often rely on decentralized digital currencies to streamline transactions and optimize operations.
To effectively merge cryptocurrency systems with manufacturing automation, manufacturers must focus on several key factors. First, aligning both technologies' infrastructure is vital for ensuring real-time, secure, and transparent transactions within the supply chain. Furthermore, understanding the necessary software integrations and blockchain protocols can enhance both operational efficiency and traceability of product flows. This process not only requires technical adjustments but also strategic planning to ensure the scalability and sustainability of the integrated system.
Steps to Integrate Cryptocurrency with Automated Manufacturing Systems
- Assess Current Infrastructure: Identify areas where automation and cryptocurrency can be introduced without disrupting existing processes.
- Select Compatible Blockchain Solutions: Choose blockchain platforms that offer scalable and secure options for real-time transactions in a manufacturing environment.
- Develop API Integrations: Ensure seamless data transfer between legacy systems and new cryptocurrency-powered automation tools through custom APIs.
- Implement Cryptocurrency Payment Solutions: Integrate cryptocurrency payment gateways to automate financial transactions in procurement and supplier management.
- Establish Security Protocols: Implement robust encryption and access control measures to protect digital transactions and sensitive data.
Potential Benefits of Integration
Benefit | Description |
---|---|
Improved Transparency | Blockchain technology ensures that all transactions are traceable, offering transparency in financial and operational processes. |
Faster Transactions | Cryptocurrency enables instantaneous cross-border transactions, reducing delays typically associated with traditional banking systems. |
Cost Reduction | Automation, coupled with cryptocurrency, reduces administrative overhead, minimizes human error, and cuts transaction fees. |
Important: When integrating cryptocurrency systems with automated manufacturing, it is crucial to maintain a flexible approach to allow for system updates and scalability in response to future technological developments.
Reducing Operational Costs with Automated Systems: A Step-by-Step Approach
In the rapidly evolving cryptocurrency landscape, businesses often face substantial operational costs. As blockchain technology and crypto-mining operations grow, manual processes and outdated systems can quickly become inefficient. By integrating automated systems, companies can streamline operations, minimize human error, and cut down on overhead. This approach is crucial not only for improving financial performance but also for enhancing overall productivity.
Automation allows for better resource allocation, reducing unnecessary labor costs and optimizing energy usage–two key concerns in the crypto industry. With the right tools and technologies, operations can be scaled up without proportionally increasing expenses, resulting in more sustainable business models.
Key Steps for Implementing Automation in Crypto Operations
- Identify Repetitive Tasks: Start by analyzing current workflows to find processes that can be automated, such as transaction processing or blockchain validation.
- Select Automation Tools: Choose software solutions or hardware that are tailored to your crypto operation's needs, like automated mining rigs or transaction monitoring systems.
- Integrate with Existing Systems: Ensure that the automation platform integrates smoothly with current infrastructure, ensuring minimal disruption during implementation.
- Monitor and Optimize: Regularly evaluate the system's performance to ensure it is providing the expected cost reductions and efficiency gains.
Important Note: Automation doesn't just save costs, it also improves system security by reducing human intervention, which can be a vulnerability in crypto operations.
Cost Breakdown Comparison
Cost Category | Manual Process | Automated System |
---|---|---|
Energy Consumption | High due to inefficiency | Optimized through smart management |
Labor Costs | Requires continuous monitoring and management | Reduced to a minimum with automated systems |
Error Handling | High risk of human error | Minimal errors due to automation protocols |
Key Insight: An effective automation strategy can cut operational costs by up to 30%, especially when focusing on energy and labor optimization.
Managing Workforce Transition in Cryptocurrency Ecosystem: Training and Reskilling for Automation
As blockchain technology and cryptocurrency platforms evolve, the need for automation in cryptocurrency-related sectors intensifies. From mining operations to decentralized finance (DeFi) platforms, automation allows businesses to enhance efficiency, reduce errors, and lower operational costs. However, the rapid shift towards automated systems also creates a significant challenge: how to reskill and retrain the workforce to adapt to this technological transition. Employees who were once engaged in manual or semi-automated tasks must now acquire new skills to remain relevant in a highly automated environment.
Successful workforce transformation in the cryptocurrency sector hinges on targeted training initiatives that equip workers with specialized knowledge. These initiatives not only cover technical skills related to blockchain, smart contracts, and security protocols but also focus on enhancing soft skills needed to manage automation tools effectively. By incorporating comprehensive learning paths and leveraging industry-specific platforms, organizations can guide employees through this transition while maintaining productivity and innovation in a highly competitive landscape.
Key Areas of Focus for Reskilling
- Blockchain Fundamentals: Employees must understand the underlying technology, including distributed ledgers and consensus algorithms.
- Smart Contract Development: Reskilling should focus on understanding the creation and management of smart contracts using platforms like Ethereum and Solana.
- Data Security and Privacy: As automation increases, so does the importance of securing blockchain transactions and user data from threats.
- AI and Machine Learning Integration: Workers should be trained in how automation tools powered by AI interact with crypto systems, optimizing trading or mining operations.
Training Approaches for Automation Adoption
- Online Certification Programs: Industry-recognized courses help employees gain theoretical and practical knowledge on blockchain technologies and decentralized systems.
- Hands-on Workshops: Interactive workshops that allow employees to engage directly with cryptocurrency mining hardware or decentralized applications (dApps) to understand how automation works in real scenarios.
- Cross-functional Collaboration: Fostering collaboration between technical teams and operations personnel to ensure a smooth transition from manual tasks to automated systems.
“The future of work in cryptocurrency lies in continuous learning. Automation may replace certain tasks, but it will also create new roles, requiring a workforce that is adaptable, skilled, and ready to innovate.”
Training Roadmap Example
Training Phase | Focus Area | Duration |
---|---|---|
Initial Awareness | Introduction to blockchain and automation in crypto | 2 weeks |
Intermediate Training | Smart contracts, security protocols, and AI tools | 4 weeks |
Advanced Skill Development | Advanced blockchain systems, dApp development, and AI integration | 6 weeks |
How Automated Systems Improve Consistency and Reduce Errors in Manufacturing
Automated systems have revolutionized manufacturing by enhancing product uniformity and reducing the likelihood of mistakes. These systems rely on precise, pre-programmed processes that can execute repetitive tasks with minimal variation, ensuring that every item produced meets the same high standard. By incorporating advanced sensors, artificial intelligence, and machine learning, automation minimizes human error, improves accuracy, and speeds up production cycles.
One of the core benefits of automation is its ability to track real-time data, adjust parameters on the fly, and detect deviations from desired specifications immediately. This proactive monitoring helps prevent defects before they can become a significant issue, resulting in improved product quality and a reduction in waste. Automated systems also allow for better resource management, ensuring consistent output while optimizing energy consumption and material usage.
Key Benefits of Automated Manufacturing Systems
- Increased Precision: Automation systems ensure exact measurements and movements, reducing variations that can occur with manual processes.
- Consistent Output: Products are made to the same specifications each time, ensuring uniformity and minimizing defects.
- Real-Time Adjustments: Automated systems can detect discrepancies in production parameters and immediately correct them to maintain product quality.
- Efficiency in Production: By eliminating manual oversight, automated systems can operate continuously without breaks, increasing throughput.
Important Insight: Automated systems enable manufacturers to detect deviations in real-time, leading to reduced defect rates and optimized production processes.
Key Steps in Enhancing Product Consistency Through Automation
- Continuous Monitoring: Automated systems monitor product parameters throughout the production process.
- Data-Driven Adjustments: With integrated analytics, systems adjust machine settings to correct any inconsistencies.
- Predictive Maintenance: Automation helps predict when equipment needs maintenance, preventing breakdowns and maintaining quality.
Benefit | Description |
---|---|
Reduced Human Error | Automation minimizes the risk of mistakes caused by fatigue, miscommunication, or manual oversight. |
Faster Production | Automated systems can operate continuously, increasing output without sacrificing quality. |
Improved Resource Utilization | Automation optimizes material and energy consumption, lowering waste and cost. |
Evaluating the Financial Impact of Automation in Manufacturing
In today's competitive manufacturing environment, automation has emerged as a powerful tool for enhancing production efficiency and reducing operational costs. However, when considering the implementation of automated systems, it is crucial to accurately assess the return on investment (ROI). ROI can significantly impact a company's decision to adopt automation, as it reflects the financial benefits in relation to the costs involved. By measuring this, manufacturers can determine the long-term sustainability and profitability of automation technologies in their operations.
Understanding the ROI of automation involves analyzing various factors such as initial investments, operational savings, and productivity improvements. It's essential to identify both tangible and intangible benefits, including labor cost reductions, enhanced precision, and minimized downtime. Moreover, assessing the ROI helps manufacturers understand when they will break even on their investments and start generating profits.
Key Factors in Calculating ROI for Automation
- Initial Investment: The upfront cost of purchasing, installing, and integrating automation systems into existing infrastructure.
- Operational Savings: Long-term savings from reduced labor, energy consumption, and maintenance costs.
- Increased Output: The ability to produce more products in less time with consistent quality.
- Reduced Downtime: Automation minimizes unplanned downtime by maintaining continuous operation.
Example ROI Calculation
Factor | Value |
---|---|
Initial Investment | $500,000 |
Annual Savings | $100,000 |
Payback Period | 5 years |
"A successful automation project doesn't just pay for itself; it transforms the way a manufacturing plant operates, unlocking further opportunities for growth and efficiency."
Understanding the potential ROI provides manufacturers with a clear picture of the financial implications and benefits of automation. By carefully considering the initial investment, long-term savings, and operational improvements, manufacturers can make well-informed decisions about implementing automation technologies to ensure a positive financial outcome.